一、Preface
The DSH double helix conical mixer is one of the most widely used and best-selling powder mixing machines. It is suitable for mixing powder (particle) materials in chemical engineering, pesticides, dyes, feed additives, pharmaceuticals, veterinary drugs, food, petroleum, metallurgy, mining, construction, machinery, national defense, and agricultural seeds. This model has the following advantages
● It has strong adaptability to the composition of materials with significant differences in weight and particle size;
● The mixing process is relatively mild and the unit energy consumption is low;
● The mixing dead corner is small, and the discharge is smooth, clean, and free of residue.
2、 Equipment structure
The structure of the DSH mixer is shown in the figure. It mainly consists of five parts: cylinder, motor reducer, transmission mechanism, spiral part, and discharge valve.
The electric motor at the top of the DSH mixer drives a two-stage double output shaft cycloidal pinwheel planetary reducer, which outputs two speeds of revolution and rotation, causing the two spiral shafts to operate in a planetary manner.
The mixing container is an inverted cone, when V< Within 10m3, the two spirals adopt a cantilever asymmetric structure, with the long spiral installed against the conical wall and the short spiral installed near the center; The diameter of the long helix is small, while the diameter of the short helix is large; Therefore, the stirring effect in the central area is greatly enhanced, and the mixing efficiency and accuracy are improved.
The transmission components of this machine adopt a multi-channel and multifunctional sealing mechanism, which can effectively prevent dust from entering the bearings and lubricating grease from seeping out and polluting materials.
3、 Working principle
During operation, the two spirals installed in the machine rotate themselves while also rotating along the conical wall, in a planetary motion. The rapid rotation of the double helix lifts the material upward, forming two asymmetric material flow along the cylinder wall and the middle from bottom to top studs;
The rotating arm drives the circular motion of the screw, causing the materials outside the screw to enter the enveloping body of the screw to varying degrees. Some materials are displaced and lifted, while the other materials are thrown out of the screw, thereby achieving continuous diffusion of materials in all circumferential directions;
The two asymmetric materials lifted to the upper part converge to the central cavity, and the two material flow converge into one downward flow, which supplements the holes of the bottom materials and forms an asymmetric cycle.
Due to the composite motion mentioned above, the materials have achieved high-precision uniform mixing in a relatively short period of time.
4、 Technical parameters
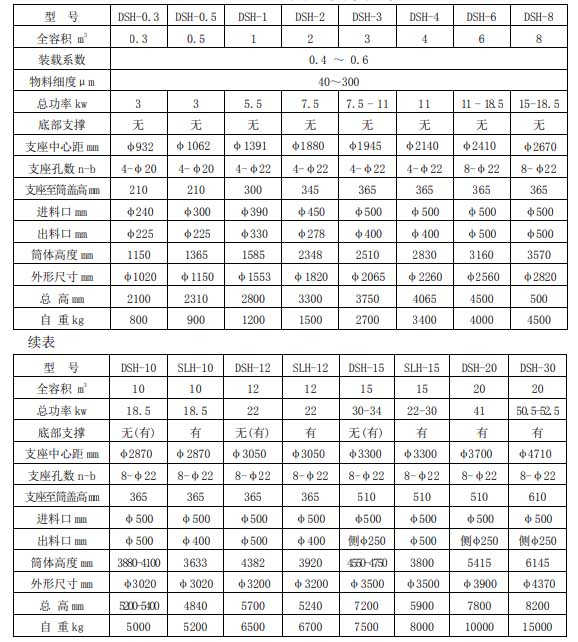
Note: The above technical parameters are for reference only and are subject to change without prior notice.
5、 Equipment lubrication
The cycloidal pin gear planetary reducer is forced lubricated by gear shaft pump or plunger oil pump. Note that the gear oil pump of the reducer must work with the main engine at the same time, and pay attention to the running direction of the oil pump. The correct direction is to flow oil from bottom to top.
The distribution box, internal gears and bearings of the transmission head are lubricated with 3 # or 4 # molybdenum disulfide grease, with a grease addition amount of 1/2 to 2/3 of the bearing space.
When this machine leaves the factory, there is no lubricating oil added to the reducer. Before starting, it is necessary to add enough lubricating oil.
The oil grade and maintenance method of the gearbox can be found in the gearbox manual.
6、 Installation and Use
● install
This machine should be installed vertically;
The ear bracket on the cone should be securely connected to the mounting bracket with bolts;
Before driving, the screw transport fixing frame inside the cylinder should be removed.
● Electrical installation
Electrical wiring and installation of switches (or control cabinets) should be carried out according to the specified power of the equipment. The switch (or control cabinet) should be placed in a prominent and convenient location, and a current overload protection device should be installed on the circuit;
For equipment with separate transmission of public and self rotation, the two motors should be interlocked to start and stop. When starting, the rotation of the spiral shaft should start before the revolution, and then start the revolution after it stabilizes; When stopping, it is required that the revolution be stopped before the rotation, or both.
● Empty start operation
After the installation of the equipment is completed, add enough oil according to the requirements of the reducer to start operation.
When the new equipment is first idling, the following points should be checked:
1. Whether each motor operates in the direction specified by the arrow
2. Whether there is friction or abnormal noise
3. Whether the operation is stable and whether there is any abnormal vibration
4. Measure whether the current value is within the specified range
5. The idle running time of the vehicle shall not be less than 30 minutes. After stopping, check the temperature rise of each transmission component of the reducer
6. Check if the oil supply to the reducer is normal
7. Check for oil leakage or seepage at the reducer, spiral drive output shaft, and flange mating surfaces
8. If any problems are found during the operation of the empty vehicle, it should be immediately stopped for inspection, and only after all issues are resolved can it be restarted
The feeding start operation can only be carried out after the empty car operation is checked and normal. The ability to start at full load depends on the characteristics of the material. Generally, small models are allowed to start at full load, while large models can be started after half of the material is added. Feeding can continue while running, and it is not allowed to start after the material has been parked for too long. If any problems are found during operation and after unloading, the machine should be immediately shut down for inspection, and can only be restarted after handling them
Requirements for apparent density of materials with different volumes:
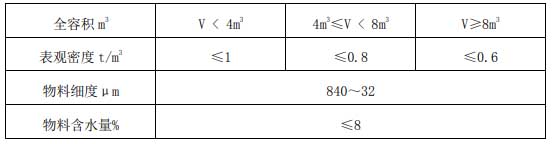
When selecting a device, the user must meet the conditions in the table above. Otherwise, it should be explained when ordering
● Determine the mixing amount of each batch of materials, and determine the processing capacity of each batch (t)=full volume (m3) × 0.6 (loading factor) × Apparent density (t/m3)
The maximum height of the material is limited to half the spiral blade that must be exposed
During equipment operation, human body and hands are not allowed to enter the machine to avoid accidents. The machine must be shut down during sampling
During operation, if hard foreign objects enter the machine or there is abnormal sound, the machine should be immediately shut down. Restart after troubleshooting
● Determination of mixing time
In general, the mixing time of each batch of materials is 8-15 minutes, and the larger the equipment, the corresponding increase in mixing time. Users can determine the accurate mixing time by sampling and analyzing at different times
● Unloading
This machine is designed to discharge without stopping the machine. After opening the valve, the material can be discharged
The discharge valve of this machine is operated separately and automatically. There are various types of discharge valves available for users to choose from when ordering
7. Maintenance
● Disassembly
When disassembling the equipment, first open the manhole cover, enter the cylinder to remove the two screws, then remove the bolts on the top cover of the cylinder, lift the reducer and the top cover of the cylinder, then remove the transmission internal parts, and finally remove all component parts for inspection, maintenance, and cleaning
The maintenance and disassembly of equipment must be carried out by professional personnel and unauthorized disassembly is not allowed
● Assembly
Assemble the machine in the opposite direction of disassembly
During assembly, each bearing and gear must be lubricated according to the equipment lubrication requirements
● Accessories
All our factory products have accessories available year-round.